Revolutionizing the Industry with Caustic Soda Pneumatic Mixing Units
In the world of industrial mixing, efficiency and reliability are paramount. One of the most significant advances in this field is the development of caustic soda pneumatic mixing units. These units have transformed how industries handle caustic soda, ensuring safety, precision, and performance. If you're a wholesale manufacturer, understanding these innovations can help you stay ahead in a competitive market.
Recent Innovations in Caustic Soda Pneumatic Mixing Unit Technology
The Future of Mixing Unit Design Trends and Predictions
Advances in Materials and Components for High-Performance Mixing Units
This blog will explore recent advancements in caustic soda pneumatic mixing unit technology, future trends, and the latest materials and components enhancing these high-performance units.
Recent Innovations in Caustic Soda Pneumatic Mixing Unit Technology
The landscape of caustic soda mixing has seen substantial changes, primarily driven by technological innovation and a better understanding of industrial needs. One of the most notable advancements is the integration of high-efficiency motors and air shuttle valves. For instance, the High-Efficiency Caustic Soda Pneumatic Mixing Unit from PRM Drilling features a 0.33 KW motor that requires minimal air, ensuring energy savings and high performance. This evolution not only maximizes production efficiency but also minimizes operational costs, making it a valuable asset for any enterprise. Safety has also been a significant focus, resulting in the development of the safety air shuttle valve. This technology ensures that the agitator operates only when the protection lid is securely closed, significantly reducing the risk of accidents. The ability to ensure safe operation without compromising on efficiency makes these units highly desirable for rigorous industrial applications. Furthermore, the advanced design and engineering behind these units allow for consistent and effective mixing results, which are critical for maintaining product quality and operational efficiency.
The Future of Mixing Unit Design Trends and Predictions
As we look ahead, the future of caustic soda pneumatic mixing units appears promising, with several trends poised to shape the industry. One significant trend is the increasing emphasis on sustainability and environmental impact. Manufacturers are now focusing on creating units that not only perform efficiently but also reduce energy consumption and emissions. This shift is driven by growing environmental regulations and the need for companies to adopt more sustainable practices. Another emerging trend is the incorporation of smart technology and IoT (Internet of Things) capabilities. Future mixing units are expected to feature advanced sensors and connectivity options that enable real-time monitoring and data analysis. This technological leap will allow operators to optimize the mixing process dynamically, leading to increased efficiency and reduced downtime. The ability to predict maintenance needs and identify potential issues before they become critical problems will revolutionize how these units are managed. Additionally, modular designs are gaining traction in the industry.
Advances in Materials and Components for High-Performance Mixing Units
The materials and components used in caustic soda pneumatic mixing units play a crucial role in their performance and longevity. Recent advancements in this area have led to the development of more durable and efficient units. For example, the use of high-quality stainless steel and other corrosion-resistant materials has significantly improved the durability of these units. This enhancement is particularly important given the corrosive nature of caustic soda, which can quickly degrade less robust materials. Modern mixing units also feature advanced sealing technologies that prevent leaks and ensure the integrity of the mixing process. These seals are designed to withstand high pressure and harsh chemical environments, further enhancing the reliability of the units. The improvements in sealing technology have also contributed to reducing maintenance requirements, as the units can operate for longer periods without needing repairs or replacements. In addition to materials, the components used in these units have also seen significant advancements. High-efficiency motors, precision-engineered gears, and advanced control systems all contribute to the superior performance of modern caustic soda pneumatic mixing units.
The advancements in caustic soda pneumatic mixing units have revolutionized the industrial mixing landscape, offering unparalleled efficiency, safety, and performance. From high-efficiency motors and safety air shuttle valves to advanced control systems and durable materials, these innovations have set new standards in the industry. Looking ahead, trends such as sustainability, smart technology, and modular designs promise to further enhance the capabilities of these units. For wholesale manufacturers, staying informed about these developments is crucial to maintaining a competitive edge. By adopting the latest technologies and best practices, businesses can ensure they are well-equipped to meet the evolving demands of the industry. To learn more about these innovations and how they can benefit your operations, consider exploring the features of the High-Efficiency Caustic Soda Pneumatic Mixing Unit from PRM Drilling.
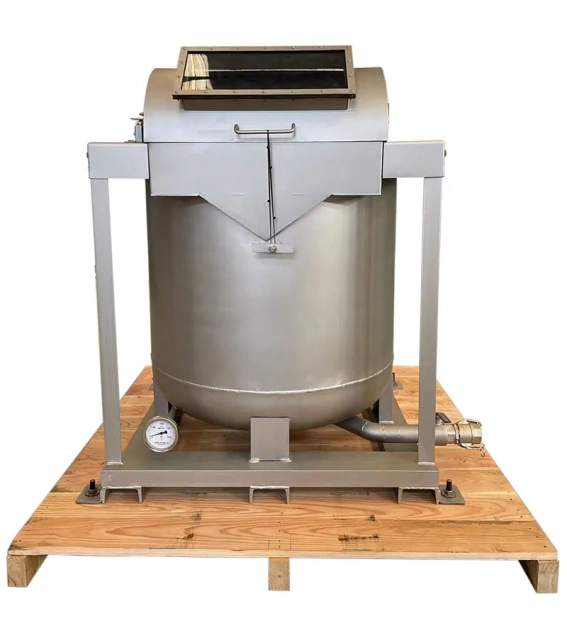
Comments
Post a Comment