Top Benefits of Foam Core Composites for UAV Manufacturers
Unmanned Aerial Vehicles (UAVs) are revolutionizing industries—from logistics to surveillance and beyond. To keep up with the demands of these high-performance applications, manufacturers increasingly rely on advanced materials like foam core composites. Lightweight, durable, and versatile, these materials are reshaping how UAVs are designed and manufactured, setting new benchmarks for efficiency and capability. Below, we explore the top benefits of using foam core composites in UAV manufacturing and why they are essential for staying ahead of the curve.
Table of contents:
Weight Reduction Benefits in Aerial Applications
How High-Strength Cores Improve Aircraft Reliability
Boosting Energy Efficiency With Advanced Foam Composites
Examples of Foam Core Success in UAV Prototypes
Weight Reduction Benefits in Aerial Applications
One of the most critical factors in UAV performance is weight. A lighter drone requires less energy to operate, leading to longer flight times, better fuel efficiency, and improved payload capacity. Foam core composites, such as Rifeng F foam, are engineered to provide high strength while drastically reducing structural weight. This closed-cell rigid foam, often made from Polymethacrylimide (PMI) polymer, boasts densities as low as 32 kg/m³ while maintaining excellent compressive strength. By minimizing unnecessary weight, foam composites allow UAVs to achieve greater flight efficiency, offering manufacturers an edge in industries where endurance and payload are essential.
How High-Strength Cores Improve Aircraft Reliability
Durability is as crucial as weight reduction when it comes to UAVs. High-strength foam core composites provide excellent impact resistance and structural integrity, even in demanding environments. These materials ensure that UAVs can withstand rough landings, high-speed flights, and varying weather conditions while maintaining performance. For example, Rifeng F cores exhibit impressive tensile and shear strength, ensuring robustness in critical components. Their ability to resist deformation under stress makes them ideal for applications that prioritize long-term reliability, from surveying remote terrains to military operations. Manufacturers seeking a dependable material for high-performance UAVs will find foam core composites an invaluable resource.
Boosting Energy Efficiency With Advanced Foam Composites
Energy efficiency is another area where foam core composites excel. By reducing weight and optimizing airflow through precise molding techniques, these materials greatly enhance a UAV's aerodynamics. Rifeng F cores are particularly advantageous because they minimize resin absorption during construction, ensuring the final product is as lightweight as possible without sacrificing strength. Furthermore, foam cores with ultra-low dielectric constants improve electronic systems' efficiency, making them ideal for UAVs that rely on advanced communication and navigation technologies. Optimized designs with foam composites not only improve power utilization but also extend operational range, contributing to overall sustainability and cost-effectiveness.
Examples of Foam Core Success in UAV Prototypes
If you're wondering how foam core composites perform in real-world scenarios, recent UAV prototypes present compelling success stories. Leading aerospace manufacturers have embraced materials like Rifeng F foam to create lightweight, robust drones capable of exceeding performance expectations. These prototypes have showcased extended flight durations, enhanced payload capacities, and improved resilience in harsh operational conditions. The customizable density and easy machinability of foam cores enable manufacturers to meet precise design needs, making them a go-to material for cutting-edge UAV engineering. Their proven track record ensures that your investment in foam composites will yield tangible improvements in performance and reliability.
Foam core composites represent the future of UAV manufacturing, offering an unbeatable combination of reduced weight, improved reliability, and enhanced energy efficiency. Materials like Rifeng F foam continue to set industry standards with their exceptional mechanical properties, paving the way for drones that perform better, last longer, and operate more efficiently. By integrating these advanced materials into your UAV designs, you not only keep up with industry demands but also position your products as leaders in innovation.For UAV manufacturers ready to elevate their designs to the next level, foam core composites are the key to unlocking new possibilities in the skies and beyond.
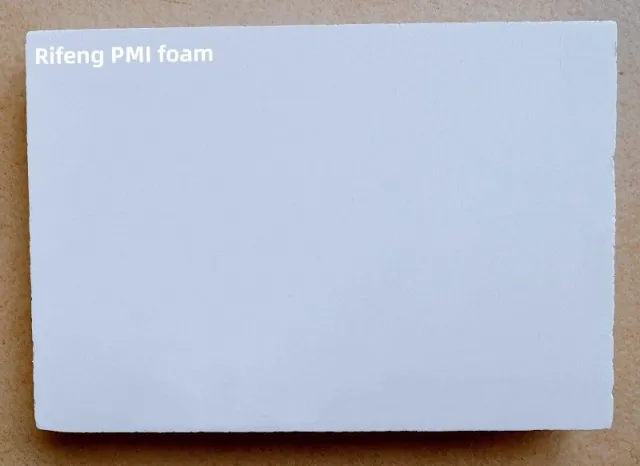
Comments
Post a Comment