The Impact of Collimator Design on Imaging Quality
Table of contents:
How Collimator Geometry Affects Image Resolution
Material Selection for Durable and Effective Collimators
Innovations in Collimator Manufacturing Techniques
Case Studies: Improved Imaging Through Advanced Collimator Design
How Collimator Geometry Affects Image Resolution
The geometry of a collimator plays a crucial role in shaping the sharpness and detail of an image. Using parallel hole collimators, which feature evenly spaced, parallel openings, ensures that only beams traveling along specific directions are utilized in creating an image. This results in reduced scatter, higher resolution, and minimized distortions. Similarly, converging collimators are excellent for magnifying distant objects, making them useful for precision imaging in both medical and industrial applications. For instance, the F-3000 collimator employs precision-engineered parallel hole technology to optimize radiation control and alignment, producing superior imaging outcomes across industries like diagnostic radiology and industrial inspection. The precise alignment and uniformity these designs impart cannot be overstated, as they play a foundational role in image quality improvements.
Material Selection for Durable and Effective Collimators
Choosing the right material for collimator construction is vital to its durability and functionality. High-quality collimators, such as the F-3000, are typically manufactured using high-density lead and aluminum alloys. These materials not only ensure long-lasting performance but also reduce secondary radiation scatter, enhancing imaging precision. High-density lead is ideal for minimizing radiation leakage, a critical factor in ensuring safety during X-ray imaging. Meanwhile, aluminum alloys lend strength and resistance to wear, making the collimator suitable for high-energy environments. Furthermore, the selection of the right materials allows for customization based on industry-specific needs, such as lightweight materials for portable imaging systems. The material composition directly contributes to the collimator's ability to consistently deliver reliable results across extended periods of use.
Innovations in Collimator Manufacturing Techniques
Technological advancements in manufacturing have drastically improved collimator efficiency and design versatility. Today, custom manufacturing allows for extreme precision in producing collimators tailored to specific requirements. Using methods like 3D printing and advanced CNC machining ensures optimized beam alignment and geometric accuracy, which is critical for scientific and industrial applications. Innovations in the design of the F-3000 collimator, for example, include low scatter technology and customizable sizes and shapes. These advancements make the device compatible with a variety of imaging systems, providing unparalleled functionality. Modern production techniques also allow for rapid prototyping, enabling manufacturers to refine designs and address custom demands with reduced lead times. The integration of these methods not only enhances imaging capabilities but also elevates the reliability, sustainability, and performance consistency of the collimator.
Case Studies: Improved Imaging Through Advanced Collimator Design
The practical advantages of advanced collimator designs are evident in numerous real-world applications. For example, in medical imaging, the F-3000 collimator has been instrumental in ensuring precise beam alignment for X-ray machines, resulting in clear diagnostic images critical for patient care. Similarly, in industrial inspection, the collimator’s ability to minimize distortion has been key to accurately detecting flaws in manufactured components. A notable case involves its use in microscopic optical alignment tasks, where the detailed parallel beams generated led to significant improvements in precision measurements. Additionally, the F-3000 has supported scientific research projects focused on laser beam alignment and optical calibration, enabling experiments to yield more accurate and reproducible results. These use cases underscore how cutting-edge collimator designs directly enhance imaging performance, paving the way for advancements in multiple domains.
Collimator design has a direct and measurable impact on the quality and precision of imaging systems across various industries. From carefully engineered geometries and the use of high-durability materials to innovative manufacturing techniques, collimators like the F-3000 exemplify how well-crafted designs can elevate imaging accuracy, safety, and efficiency. Whether it’s for medical diagnostics, scientific research, or industrial inspection, the importance of a high-quality collimator cannot be overstated. Understanding these design principles and leveraging advanced tools like the F-3000 allows organizations to optimize their imaging processes and unlock the full potential of their applications.
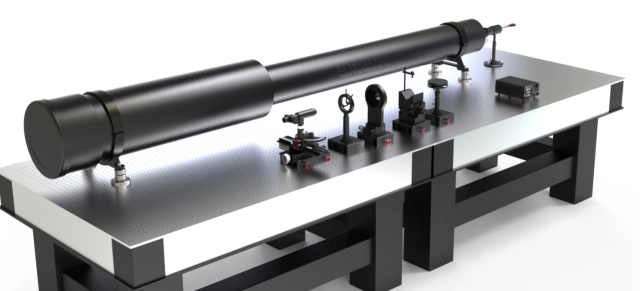
Comments
Post a Comment